Screw type and Reciprocating type Compressor
Recommendation (Regular Routine Oil Analysis)
CompressorCheck™ 804 |
CompressorCheck™ 834 |
All Tests below are for CompressorCheck ™ 804
Wear Metal Elements -Condition
- Fine Wear Metal - 18 elements, ASTM D6596 or ASTM D5185
- RFS Coarse Wear Metal - 11 elements, ASTM D6595
- Particle Quantifier Index (PQ Index), ASTM D8184
Oil Condition
- Oil Condition; oxidation, nitration, ASTM E2412M
- Viscosity @40°c or 100°c, ASTM D445
- Acid Number, ASTM D974
Contamination
- Oil Contamination; dirt & dust, etc, ASTM D6595 or ASTM D5185
- %Moisture & Water, ASTM D6304
- Wrong oil contamination
|
- Report with interpretation
|
|
All Tests below are for CompressorCheck ™ 834
Wear Metal Elements -Condition
- Fine Wear Metal - 18 elements, ASTM D6596 or ASTM D5185
- RFS Coarse Wear Metal - 11 elements, ASTM D6595
- Particle Quantifier Index (PQ Index), ASTM D8184
Oil Condition
- Oil Condition; oxidation, nitration, ASTM E2412M
- Viscosity @40°c or 100°c, ASTM D445
- Acid Number, ASTM D974
Contamination
- Oil Contamination ; dirt & dust, ASTM D6595 or ASTM D5185
- %Moisture & Water, ASTM D6304
- Wrong oil contamination
- Insoluble -Contamination , ASTM D4898M
(Gravimetric Analysis)
|
- Report with interpretation
|
|
Highlight FocusLab's unique testing
in CompressorCheck™ 804
|
Highlight FocusLab's unique testing
in CompressorCheck™ 834
|
Note: The above recommended test package will be guideline, the suitable test package may be vary depend upon right application, environment severity, critical factor, machine age, and so on.
Centrifugal type Compressor or Turbo Compressor
Recommendation (Regular Routine Oil Analysis)
CompressorCheck™ 894 |
CompressorCheck™ 813 |
All Tests below are for CompressorCheck ™ 894
Wear Metal Elements -Condition
- Fine Wear Metal - 18 elements, ASTM D6596 or ASTM D5185
- RFS Coarse Wear Metal - 11 elements, ASTM D6595
- Particle Quantifier Index (PQ Index), ASTM D8184
Oil Condition
- Oil Condition; oxidation, nitration, ASTM E2412M
- Viscosity @40°c or 100°c, ASTM D445
- Acid Number, ASTM D974
Contamination
|
- Report with interpretation
|
|
All Tests below are for CompressorCheck ™ 813
Wear Metal Elements -Condition
- Fine Wear Metal - 18 elements, ASTM D6596 or ASTM D5185
- RFS Coarse Wear Metal - 11 elements, ASTM D6595
- Particle Quantifier Index (PQ Index), ASTM D8184
Oil Condition
- Oil Condition; oxidation, nitration, ASTM E2412M
- Viscosity @40°c or 100°c, ASTM D445
- Acid Number, ASTM D974
Contamination
|
- Report with interpretation
|
|
Highlight FocusLab's unique testing
in CompressorCheck™ 894
|
Highlight FocusLab's unique testing
in CompressorCheck™ 813
|
Note: The above recommended test package will be guideline, the suitable test package may be vary depend upon right application, environment severity, critical factor, machine age, and so on.
Compressor type Application
- Centrifugal Compressor (air /gas) critical and severe operation , start up , commisioning
- Turbo Compressor
Advanced Package
CompressorCheck™ 823 |
All Tests below are for HydraulicCheck ™ 823
Wear Metal Elements -Condition
- RDE - AES Wear Metal - 18 elements, ASTM D6595
or ICP - AES Wear Metal - 18 Elements, ASTM D5185
- RFS Coarse Wear Metal - 11 elements, ASTM D6595
- Particle Quantifier Index (PQ Index), ASTM D8184
- Ferrographic Analysis, ASTM D7690
Oil Condition
- Oil Condition; oxidation, nitration, ASTM E2412M
- Viscosity @ 40°c or 100°c, ASTM D445
- Acid Number, ASTM D974
Contamination
|
- Report with interpretation
|
|
Highlight FocusLab's unique testing
in HydraulicCheck™ 823
|
|
Product Data & Service Sheet of CompressorCheck TM 823 |
|
* Wrong oil contamination can be detected in case BASELINE data will be available
Note: The above recommended test package will be guideline, the suitable test package may be vary depend upon right application, environment severity, critical factor, machine age, and so on. |
Test Description
Oil Sample Quantity: 200 ml.
Oil Sampling Location/Point
- Follow OEMs recommended sampling location / point
- In the absence of OEMs guidelines , recommended below for general guidance for sampling point /location
Possible location/point will be
Compressor-screw type
- Sampling after oil/water separation line and before filter location -location A
by drop tube -vacuum pump
and/or
- Sampling at Filter Housing (upstream of filter) - point B as below picture
By installing valve or minimess valve
|
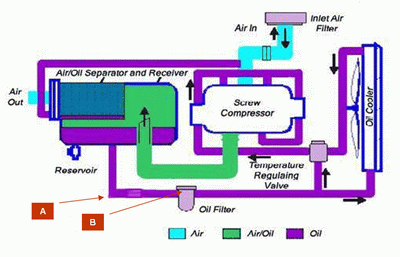 |
Compressor-Centrifugal type
- Through sample valve installed upstream of the filter on the return line
|
Sampling Tools & Devices
Sampling Techniques
Sampling Frequency
- Initially , follow OEMs recommended sample interval for your equipment
- In the absence of OEMs guidelines , recommended below for general guidance in establishing sample interval.
Recommended Sampling Frequency (Sampling Interval)
Industry - Application |
Normal Use |
Intermittent Use |
Screw ,Rotary,Reciprocating
Centrifugal |
500 hours
or one month
and just prior to oil drain |
Quarterly
and just prior to oil drain |
Reports
LubeCheck™ Oil Analysis Report provide :-
- Display an easy-to-read and understand.
- Information for wear condition ,lubricant condition and contamination.
- Interpretation and recommendation of the result . Option for Bilingual.
- Color coded display of overall condition for present sample and history condition of previous sample.
|
|
- Color coded problem highlights.
- Provide new oil or reference oil for comparing result and as baseline.
- Publish Alarm Limit range of the equipment and oil.
- Comprehensive trending graph of most parameters.
- LubeCheck™ Oil Analysis offers reporting options via internet, email and fax.
|
|
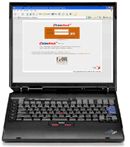
 |
Turnaround Time Service
The report is typical available within 7-10 working days of sample receipt at FocusLab's labortory. Examples of report
Remarks: Oil samples (after completion of testing) will be retained in our laboratory for approx 60 days ,just in case of in-depth testing and/or any future purpose. |
|
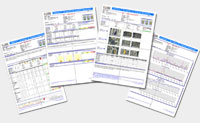 |
Technical articles and case study related to this application
|
“Analyzing compressor lubricant is an important part of maintaining and restoring a refrigeration / air conditioning system" |
|
|
|
Reference Source : SIEMENS Building Technologies -website |
|
|
|