Recommendation (Regular Routine Oil Analysis)
GearCheck™ 804 |
GearCheck™ 884 |
All Tests below are for GearCheck ™ 804
Wear Metal Elements -Condition
- Fine Wear Metal - 18 elements, ASTM D6595 or ASTM D5185
- RFS Coarse Wear Metal - 11 elements, ASTM D6595
- Particle Quantifier Index (PQ Index), ASTM D8184
Oil Condition
- Oil Condition; oxidation, nitration, nitration, ASTM E2412M
- Viscosity @ 40°c or @ 100°c, ASTM D445
- Acid Number, ASTM D974M
Contamination
- Oil Contamination; dirt & dust, etc
- % Moisture & Water, ASTM D6304
- Wrong oil contamination
- Report with Interpretation and Recommendation
|
|
All Tests below are for GearCheck ™ 884
Wear Metal Elements -Condition
- Fine Wear Metal - 18 elements, ASTM D6595 or ASTM D5185
- RFS Coarse Wear Metal - 11 elements, ASTM D6595
- Particle Quantifier Index (PQ Index), ASTM D8184
- Ferrography Analysis, ASTM D7690M
Oil Condition
- Oil Condition; oxidation, nitration, nitration, ASTM E2412M
- Viscosity @ 40°c or @ 100°c, ASTM D445
- Acid Number, ASTM D974M
Contamination
- Oil Contamination; dirt & dust, etc
- % Moisture & Water, ASTM D6304
- Wrong oil contamination
- Report with Interpretation and Recommendation
|
|
Highlight FocusLab's unique testing
in GearCheck™ 804
|
Highlight FocusLab's unique testing
in GearCheck™ 884
|
Note: The above recommended test package will be guideline, the suitable test package may be vary depend upon right application, environment severity, critical factor, machine age, and so on.
Gear System Application |
- High Precision and Reliability -Gear System
- High Speed -Gear System
- High Performance -Gear System
- Power Turbine Gear Ssystem
- Wind Turbine -Gear System
- Gear Oil -lubricating Compartment /System
- Transmission - lubricating Compartment/System
|
All Tests below are for GearCheck 824
Wear Metal Elements -Condition
- Fine Wear Metal - 18 elements, ASTM D6595 or ASTM D5185
- RFS Coarse Wear Metal - 11 elements, ASTM D6595
- Particle Quantifier Index (PQ Index), ASTM D8184
- Ferrography Analysis, ASTM D7690M
Oil Condition
- Oil Condition; oxidation, nitration, nitration, ASTM E2412M
- Viscosity @ 40°c or @ 100°c, ASTM D445
- Acid Number, ASTM D974
Contamination
|
|
Highlight FocusLab's unique testing
in GearCheck™ 824
|
Test Description
Oil Sample Quantity: 100 ml.
Oil Sampling Location/Point
- Follow OEMs recommended sampling location / point
- In the absence of OEMs guidelines , recommended below for general guidance for sampling point /location
- Drain plug/Line with tube extender
At drain line /tube /valve , modification by install pivot or Tubing sampling valve
|
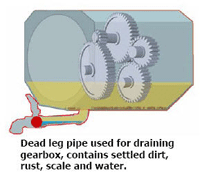
Before modification
|
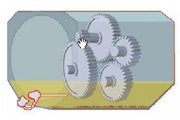
After modification |
Tubing sampling valve
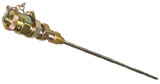 |
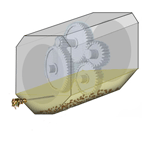 |
Avoid to take sample from drain line.
|
- Dedicated sampling valve installed in case wet sump circulating system , pressure feed line if pump feed
|
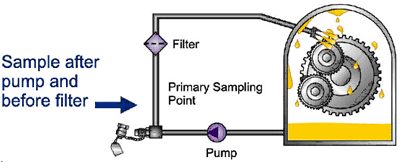
|
- Other gear systems, consult FocusLab technical experts.
|
Sampling Tools & Devices
Sampling Techniques
Sampling Frequency
- Initially , follow OEMs recommended sample interval for your equipment
- In the absence of OEMs guidelines , recommended below for general guidance in establishing sample interval.
Recommended Sampling Frequency (Sampling Interval)
Industry - Application |
Hours |
Kilometers |
Highway
(Gear, differential, transmissions) |
|
20,000 kms
and just prior to oil drain |
Off-Highway
(Gear, differential, transmissions) |
500 hours
and just prior to oil drain |
|
Marine
Gear - Main Propulsion System
Reduction gear |
500 hours
or one month
and just prior to oil drain |
|
Gear - Supporting System
Deck Gear Drive |
2,000 hours
or quarterly
and just prior to oil drain |
|
Industry - Application |
Normal Use |
Intermittent Use |
Industry
Gear - low speed |
Bi-monthly, 1,000 hours
and just prior to oil drain |
Quarterly
and just prior to oil drain |
Gear - high speed |
Monthly, 300-500 hours
and just prior to oil drain |
Quarterly
and just prior to oil drain |
Reports
LubeCheck™ Oil Analysis Report provide :-
- Display an easy-to-read and understand.
- Information for wear condition ,lubricant condition and contamination.
- Interpretation and recommendation of the result . Option for Bilingual.
- Color coded display of overall condition for present sample and history condition of previous sample.
|
|
- Color coded problem highlights.
- Provide new oil or reference oil for comparing result and as baseline.
- Publish Alarm Limit range of the equipment and oil.
- Comprehensive trending graph of most parameters.
- LubeCheck™ Oil Analysis offers reporting options via internet, email and fax.
|
|
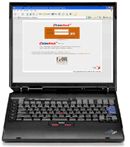
 |
Turnaround Time Service
The report is typical available within 7-10 working days of sample receipt at FocusLab's labortory. Examples of report
Remarks: Oil samples (after completion of testing) will be retained in our laboratory for approx 60 days ,just in case of in-depth testing and/or any future purpose. |
|
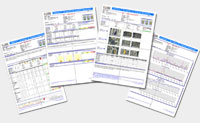 |
Technical articles and case study related to this application
|
|
|
Ken Nicholas, Schroeder Industries; Richard Winslow, Pacificorp - Naughton Plant
Ted Naman, ConocoPhillips
Practicing Oil Analysis Magazine . November 2006 |
|
|
|