Recommendation ( Regular Routine Oil Analysis)
All Tests below are for HeattransferCheck™819
Corrosive, Rust & Metal
Elements - Condition
- Corrosive and Rust Metal Elements, ASTM D5185
(Iron, Copper, Aluminium, Tin, Lead)
Fluid Condition
- Viscosity @ 40 °c, ASTM D445
- TAN (Total Acid Number) , ASTM D974 or ASTM D664
Thermal Stability
- Low Boilers (LB)%, ASTM D6743
- High Boilers (HB)%, ASTM D6743
Safety in Use Condition
- Flash Point, °c, ASTM D92
- Fire Point, °c, ASTM D92
- Auto-Ignition Temperature, °c, ASTM E659
Contamination Condition
- Contamination; Silicon, Sodium, ASTM D5185
- %Moisture & Water, ASTM D6304
- Insoluble Solids, mg/100g, ASTM D4898M
|
- Report with interpretation & recommendation
|
|
Note: The above recommended test package will be guideline, the suitable test package may be vary depend upon right application, environment severity, critical factor, machine age, and so on.
Test Description
Oil Sample Quantity: 500 ml.
Oil Sampling Location/Point
- Follow OEMs recommended sampling location / point
- In the absence of OEMs guidelines , recommended below for general guidance for sampling point /location
Possible location/point and technical concerns will be
- Good sample shall be the most representative of the heat transfer fluid system.
and
- Good sample must be taken from a live part /zone of the system.
and
- Good location from which to take sample include a low -point drain near the pump or heater
or the blow-down valve mounted on the Y-strainer. The Y-strainer is usually located in the return line
just upstream of the pump suction.
- Ideally, the fluid sample shoud be taken from the system between 80 c (176 f ) to
130 c (266 f ).
and/or
- To take the sample after the system has been on standby (the pump's still running but the
fluid has cool down)
- If the fluid sample is too hot , it will not only smoke but also the acid number may be
indicate artificial high acid level due to oxidation during the sampling process . As well as
this practice is considerably safer .
|
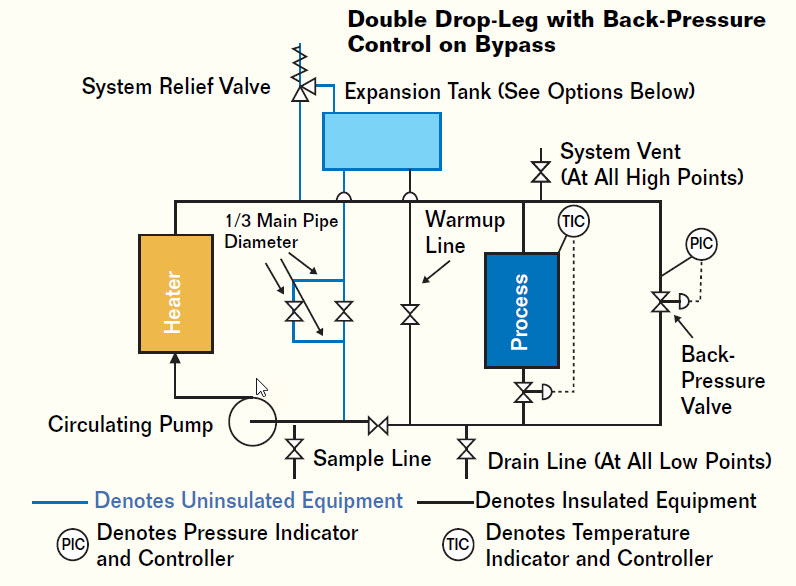
Picture 1 Double Drop Leg with back pressure control on by-pass
|
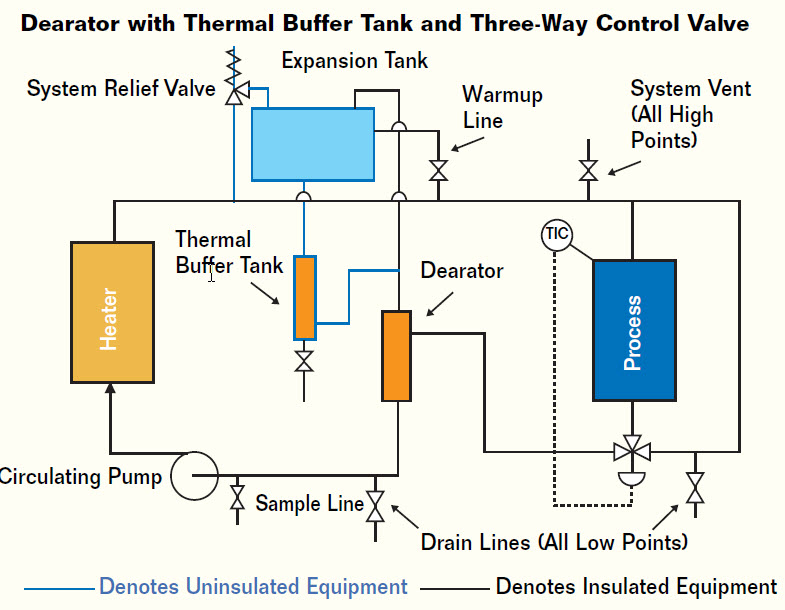
Picture 2 Dearator with Thermal Buffer Tank and 3-way control valve
|
Note:
- Make sure that the pump has been running so that the sfluid you sample is truly representative
of the fluid in the heat trasnfer fluid
- Flushing the valve properly in order to remove excess contaminants.
- Samples taken from the expansion tank ,or from a dead leg/zone are not representative of the system.
|
Sample Kits
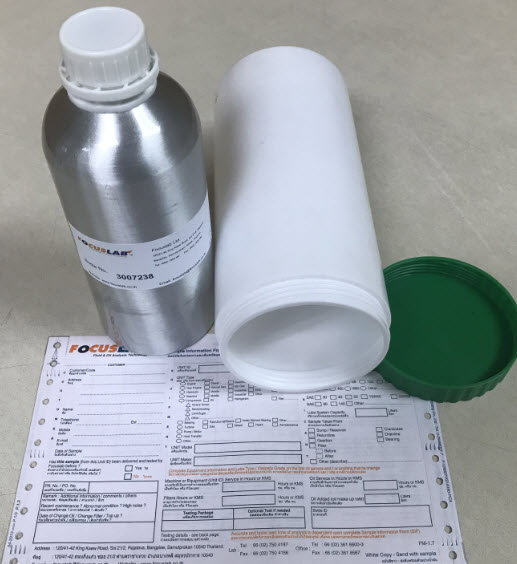
Sampling Frequency
- Initially , follow OEMs recommended sample interval for your equipment
- In the absence of OEMs guidelines , recommended below for general guidance in establishing sample interval.
- In general , recommend to take sample every 6 month
Reports
HeatTransferCheck™ Oil Analysis Report provide :-
- Display an easy-to-read and understand.
- Information for wear condition ,lubricant condition and contamination.
- Interpretation and recommendation of the result . Option for Bilingual.
- Color coded display of overall condition for present sample and history condition of previous sample.
|
|
- Color coded problem highlights.
- Provide new oil or reference oil for comparing result and as baseline.
- Publish Alarm Limit range of the equipment and oil.
- Comprehensive trending graph of most parameters.
- HeatTransferCheck™ Oil Analysis offers reporting options via internet, email and fax.
|
|
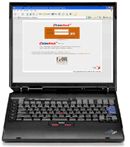
 |
Turnaround Time Service
The report is typical available within 7-10 working days of sample receipt at FocusLab's labortory. Examples of report
Remarks: Oil samples (after completion of testing) will be retained in our laboratory for approx 60 days ,just in case of in-depth testing and/or any future purpose. |
|
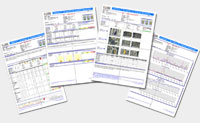 |
Technical articles and case study related to this application
Department of Industrial Works, Minstry of Industry
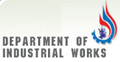
Thailand Law and Regulation
|
|