Overview
Oil is the lifeblood of machines and equipment.
Oil Analysis can identify performance or condition of machines and equipment from determining degree of wear (normal or abnormal), degree of oil degradation and degree of oil contamination.
The goal of oil analysis program is, help to increase reliability and availability of machines and equipment while minimizing maintenance budget and cost which associated with lubrication failure mode, labor, downtime etc.
|
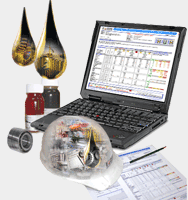 |
Benefit of Oil Analysis
Short-term Benefits
There are five key areas in which a regular-routine oil analysis will benefits in the short-term:
|
- Know oil condition whether it is suitable for continued use
- Know machines or equipment condition:
- Troubleshoot machines and equipment problem
- Determine projected time to serious failure
- Evaluate machines and equipment prior to a major shutdown
- Spot-check on regular basis or Preventive Maintenance (PM) Program
- Support Root Cause Analysis.
|
|
Long-term Benefit
After a long period of implementing regular-routine oil analysis, there are eight key areas in which routine oil analysis will benefit in the long-term: |
- Trend line analysis to identify problems in the early stage
- Monitor extended oil drain intervals
- Able to plan & make repair or replace decisions
- Create new, rebuild or repair acceptance specifications
- Identify poor maintenance or repair practices & procedures
- Identify excessive operating conditions
- Support warranty claims
- Support Root Cause Analysis
|
|
Principle of Oil Analysis
A well-designed routine oil analysis testing and result must encompass three categories:
Wear Condition (Wear Metal Debris);
- Wear debris analysis relate to health of machine
Oil Condition (Fluid Properties);
- Oxidation , Nitration
- Total Acid Number (TAN)
- Total Base Number (TBN) etc.
Contamination (Fluid Contamination);
- Dirt & Dust
- Fuel
- Coolant
- Wrong oil
- Particle contamination
- etc.
|
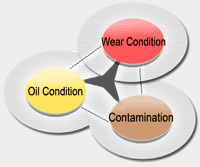 |
Recommendation and Interpretation will be done by considering from the three categories, machine in service hours, oil in service hours, and related operating information, such as oil change/make up, filter change etc.
Start and Design Oil Analysis Program
Success in oil analysis program requires a commitment to truly understand the following steps and implementation:
- Select machines and equipment to be implement an Oil Analysis Program
- Select and consider Routine Testing and Extra Test
|
Application of Oil Analysis (Machine Type and testing) |
|
|
- Sampling Method
- Target and Limit Setting
- Review Data - Report
- Interpret Data and make decisions on continuous improvement
|
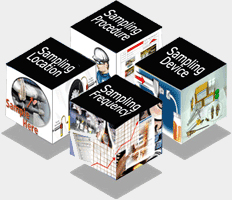 |
Report -Oil Analysis
Alarm Limit (Warning Limit)
The primary of alarm or alarm limit , is to filter (funnel) data so that the data end-users spend their time managing and correcting exceptional situations instead of perusing the data trying to find exceptions. The alarm serves as "trip-wire" to tell the analysts that a threshold has been passed and that the action is required. Some data parameters have only limits such as Wear Metal Debris (RDE,RFS ,TAN). A few data parameter employ lower limits like TBN ,flash point . Other parameters like viscosity use both upper and lower limits.
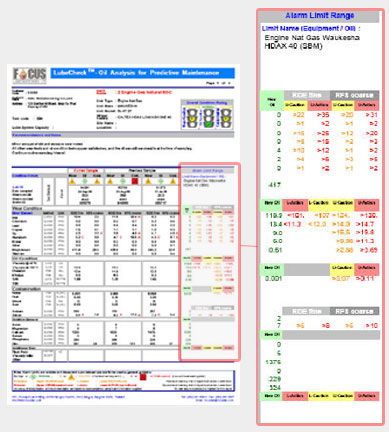
Learn more about Alarm Limit >> Training
Key to effective and successful Oil Analysis Program
Oil Analysis has worldwide proven to be an effective monitoring tool to help increase reliability and availability, but unfortunately, different organizations or plants have achieved a variety degrees of success and economical benefits.
Briefly, effective and successful Oil Analysis Program requires an understand and drive the program, organized, sustained and improved efforts .
|